RESOURCES
Home » CIMT2025 Successfully Concludes | Honoring a Better Life with Advanced Technology, Charting a New Journey
CIMT2025 Successfully Concludes | Honoring a Better Life with Advanced Technology, Charting a New Journey
Table of Contents
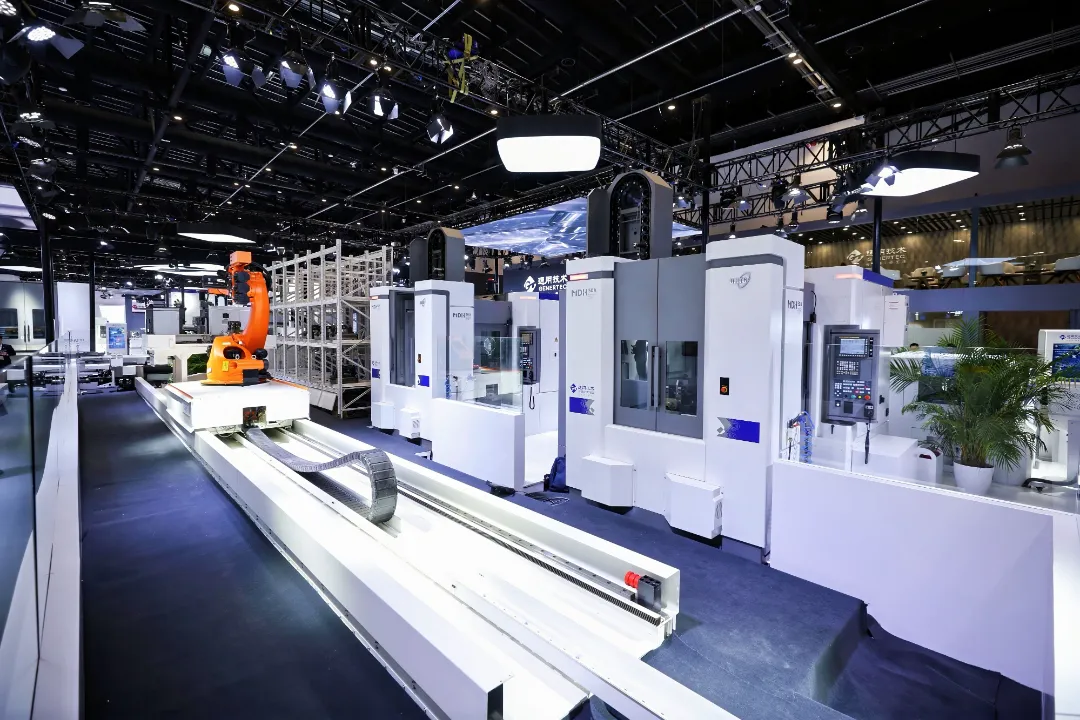
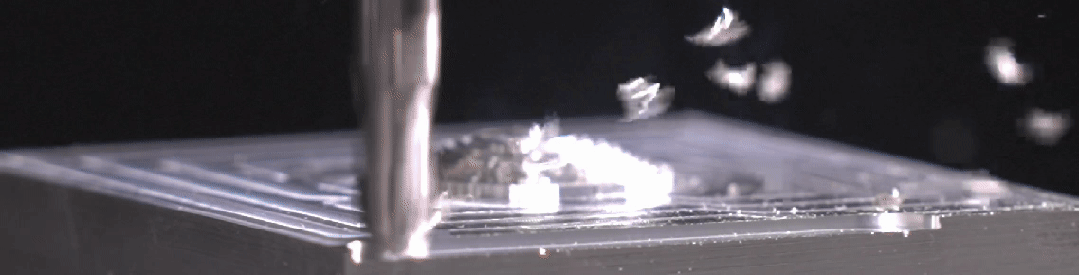
On April 26, the 19th China International Machine Tool Show (CIMT2025) successfully concluded in Beijing. Under the theme "Honoring a Better Life with Advanced Technology," Genertec Group showcased several new high-end CNC machine tools, attracting significant attention from industry experts and customers. The exhibition highlighted the Group’s strong technological capabilities and innovation achievements in the high-end machine tool sector. During the event, the Group’s booth received over 6,000 domestic and international visitors, with total signed contracts exceeding 500 million yuan.
At this exhibition, Genertec Group showcased a total of 29 high-end, intelligent, and green machine products, including 22 machine tool units, 3 models, 4 measuring instruments, and 8 types of functional components, offering a wide range of high-quality, advanced machine tools and full-chain intelligent manufacturing solutions. Among them, 13 products are directly serving key national sectors, demonstrating the Group’s strong commitment to supporting the development of national industries.
1.RAFP20/L30-T Thermoplastic Robotic Fiber Placement Machine
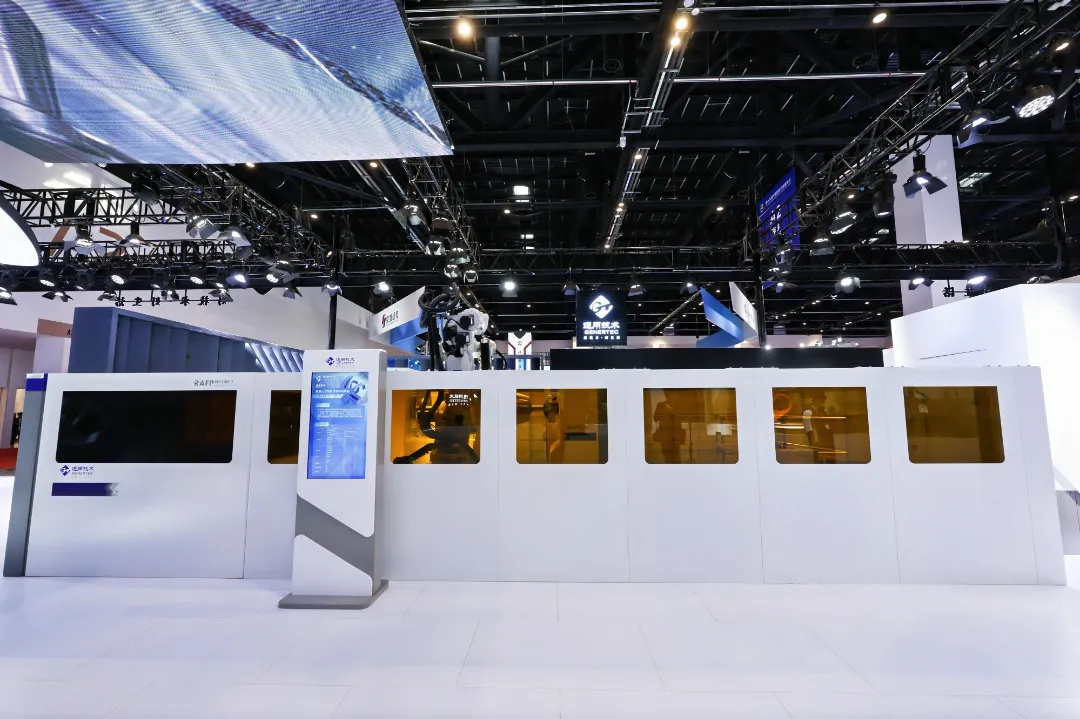
This product is a specialized piece of equipment independently developed by Genertec Group, primarily used for the automated placement of thermoplastic composite components. It is equipped with a high-power continuous laser heating system, combined with closed-loop temperature monitoring sensors and mold constant-temperature field control, enabling high-temperature forming and in-situ curing of thermoplastic composites. Utilizing multi-axis coordinated control, the fiber placement head can be quickly exchanged, meeting the requirements for automatic placement of complex curved surfaces with both thermoplastic and thermoset materials across multiple processes.
2.HMU200400PF Parallel Tilting Five-Axis Machining Center
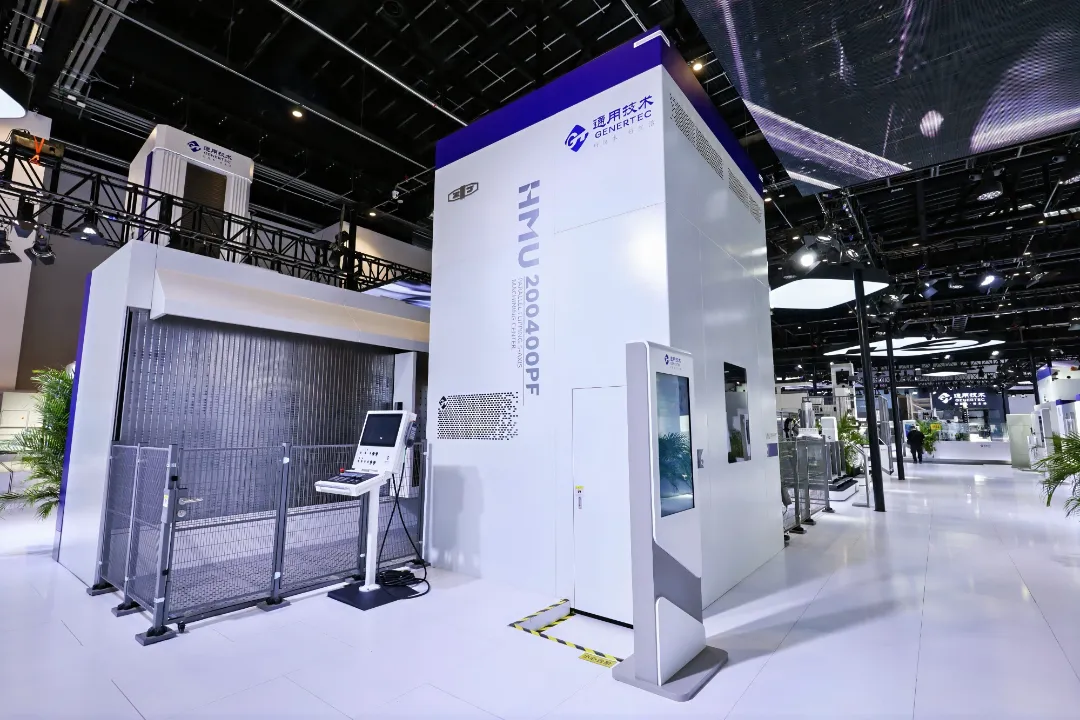
This product is designed for the efficient and precise machining of thin-walled aluminum alloy structural components. It features high efficiency, high precision, and fast response, making it ideal for processing a variety of medium to large parts in small to medium batches with high accuracy requirements. The product adopts a modular design with a wide range of configurations to fully meet various user machining needs. It is equipped with a three-link parallel mechanism that enables rapid adjustment of tool orientation, and a specially customized high-rigidity ball joint structure to ensure high static and dynamic rigidity as well as excellent reliability. The machine also features dual loading/unloading stations and a tilting platform mechanism, allowing for horizontal clamping and vertical machining of parts, thereby enhancing processing efficiency and facilitating automation and production line upgrades. Additionally, it is equipped with a flexible robotic tool magazine, offering strong scalability. This product is widely applicable for the efficient and precise machining of medium to large thin-walled aluminum alloy structural components.
3.SMU350 Blade 5-Axis Machining Center
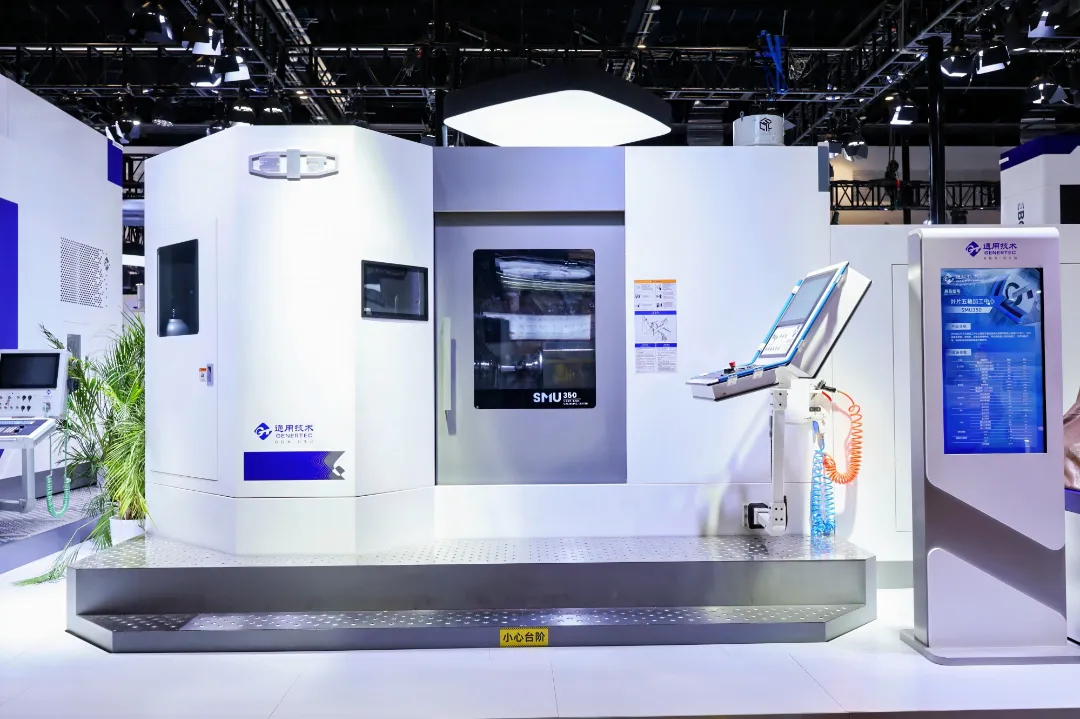
The SMU350 adopts an overall vertical structure with a separated-axis layout, featuring excellent dynamic performance. It is designed for high-precision and high-efficiency machining of complex blade surfaces. This product offers high speed, high precision, high stability, and superior dynamic response, coupled with powerful cutting capabilities.
It enables the complete machining of blade profiles, blade crowns, damping platforms, edges, and blade roots in a single setup, covering both semi-finish and finish milling processes.
The SMU350 is widely applicable to the precision machining of difficult-to-cut materials such as stainless steel, aluminum alloys, titanium alloys, and high-temperature alloys.
4.YP70 Blade Measurement Machine
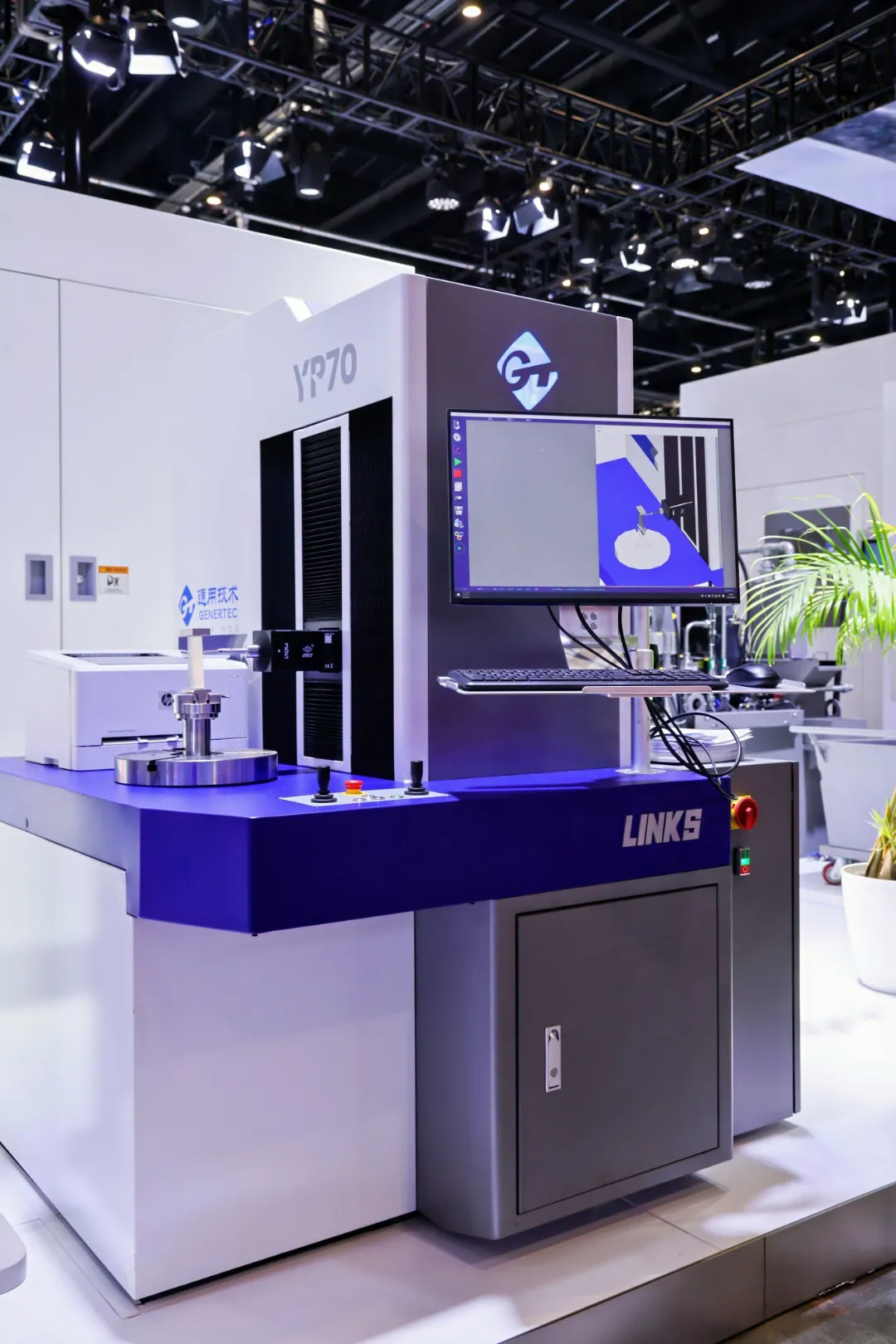
The YP70 utilizes virtual measurement and digital twin technologies to construct high-precision digital models of blades. By integrating a 3D model visualization and interaction system with a high-speed four-axis linkage scanning measurement system, it achieves real-time synchronized comparison between the digital twin and the physical blade.
Equipped with a self-developed blade quality analysis module, the system forms an integrated closed-loop inspection platform. It successfully overcomes technical bottlenecks in high-flexibility adaptation, high-cycle response, and high-precision inspection for engine blade profile accuracy.
All core functional components and key technologies of this equipment are fully independently developed, achieving 100% autonomy and controllability.
5.VMU63P Vertical 5-Axis Machining Center
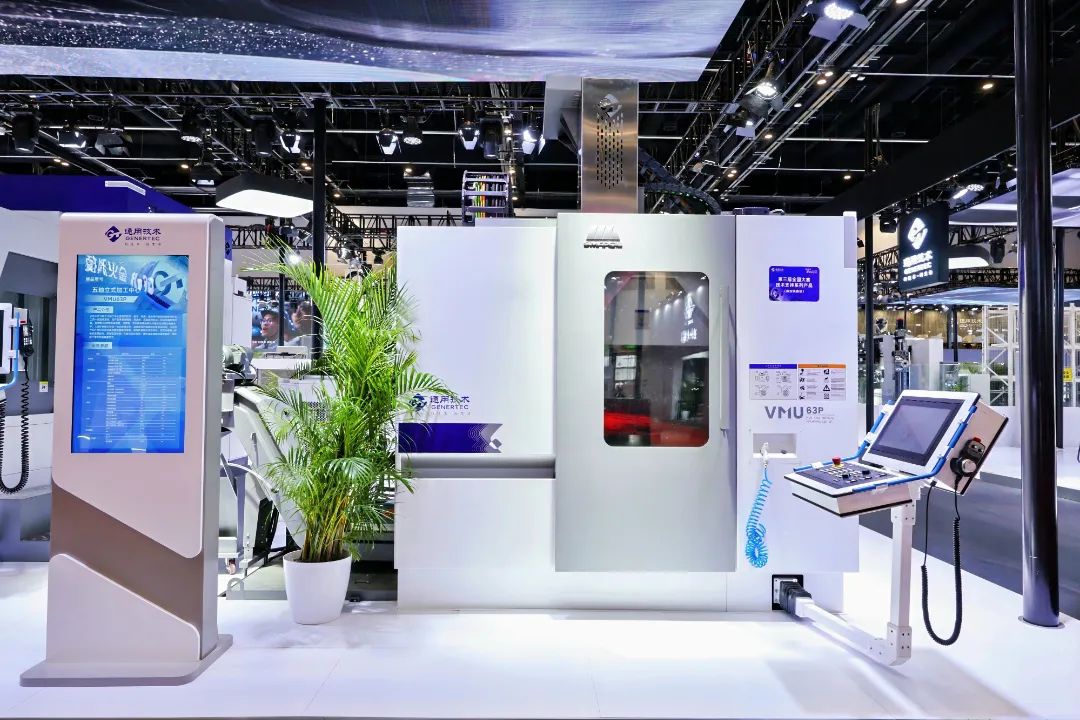
The VMU63P is a high-performance vertical 5-axis machining center independently developed for industries such as energy, mold, and automotive manufacturing.
It features rapid linear axis traverse speeds up to 60 m/min, acceleration up to 1G, and rotary axes directly driven by torque motors with speeds exceeding 50 rpm.
The machine’s bed and column are integrally cast using engineered mineral composite materials, providing excellent vibration damping and thermal deformation resistance.
With its characteristics of high speed, high precision, and high rigidity, along with a rich array of configurations and powerful 5-axis simultaneous machining capabilities, the VMU63P fully meets the demands of machining complex and irregular-shaped components.
It features rapid linear axis traverse speeds up to 60 m/min, acceleration up to 1G, and rotary axes directly driven by torque motors with speeds exceeding 50 rpm.
The machine’s bed and column are integrally cast using engineered mineral composite materials, providing excellent vibration damping and thermal deformation resistance.
With its characteristics of high speed, high precision, and high rigidity, along with a rich array of configurations and powerful 5-axis simultaneous machining capabilities, the VMU63P fully meets the demands of machining complex and irregular-shaped components.
6.UPT250B Ultra-Precision Single-Point Diamond Turning Machine
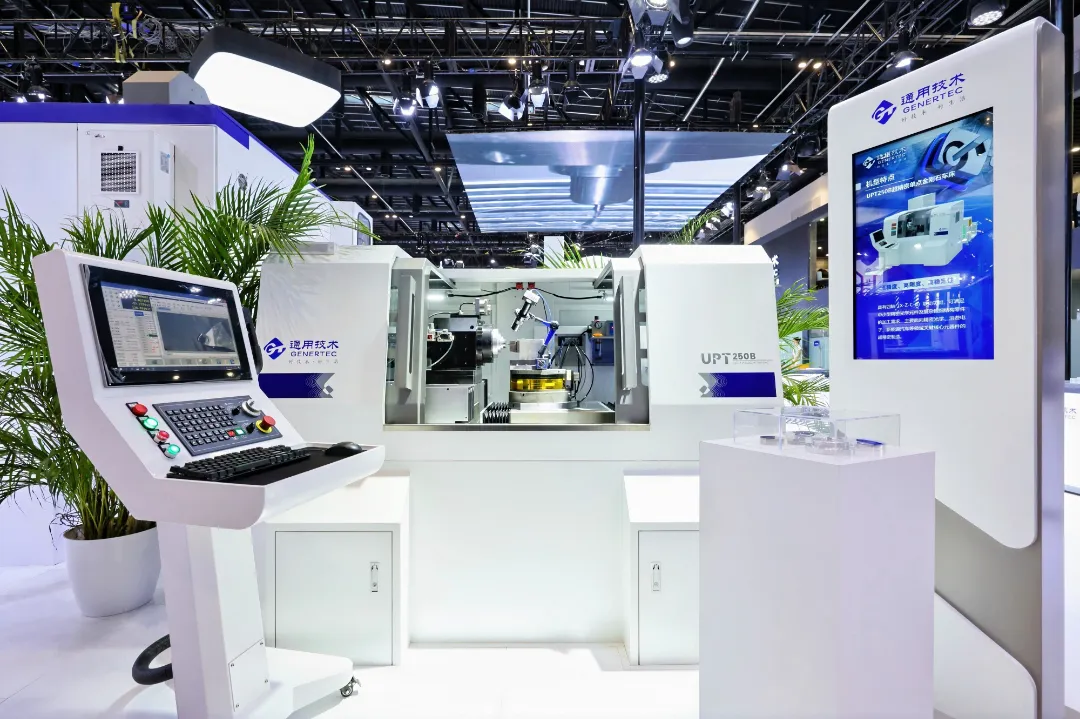
The UPT250B is primarily used for precision machining of components in industries such as optoelectronics, medical devices, and photovoltaic and solar thermal technologies.
The machine adopts a T-type layout and features fully constrained ultra-precision hydrostatic guideways, a high-rotational-accuracy spindle unit, and an ultra-precision rotary worktable.
It is capable of ultra-precision turning, grinding, and fly-cutting of various complex surface components.
The machine bed is supported by a high-performance air spring vibration isolation system, effectively isolating high-frequency vibrations.
The protection system is designed separately from the machine body to minimize external system interference during machining.
The machine adopts a T-type layout and features fully constrained ultra-precision hydrostatic guideways, a high-rotational-accuracy spindle unit, and an ultra-precision rotary worktable.
It is capable of ultra-precision turning, grinding, and fly-cutting of various complex surface components.
The machine bed is supported by a high-performance air spring vibration isolation system, effectively isolating high-frequency vibrations.
The protection system is designed separately from the machine body to minimize external system interference during machining.
7.GMC2550wsμ Moving Table and Moving Beam Type Gantry 5-Face Machining Center
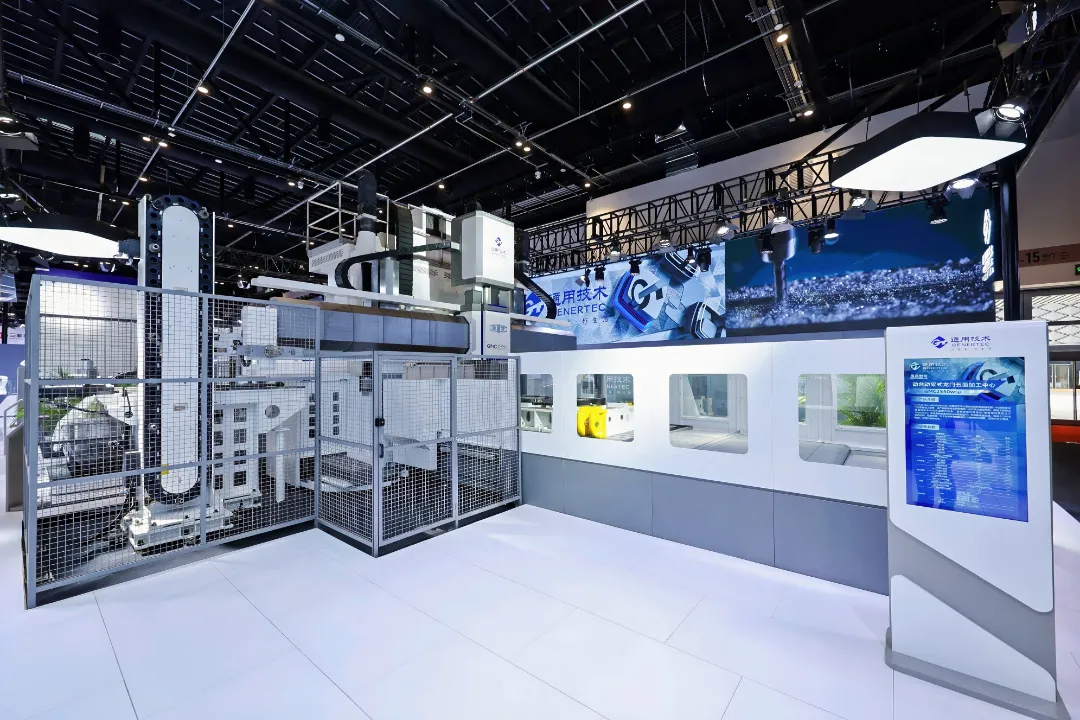
The GMC2550wsμ is mainly used in industries such as machine tool manufacturing, mold making, energy, shipbuilding and offshore engineering, and construction machinery.
The machine adopts a modular design with a moving table and moving beam configuration, providing excellent structural rigidity.
It is equipped with a self-developed, integrally cast, hardened rolling guideway system made of cast iron, whose high rigidity and low friction ensure superior linear and positioning accuracy.
A servo-driven constant-temperature control system guarantees long-term high-precision and stable operation.
The machine features a self-developed high-speed, high-torque mechanical spindle system and a wide variety of fully automatic attachment milling heads, with optional through-spindle coolant (TSC) capability to meet diverse application scenarios.
It is also equipped with a vertical-horizontal switching tool magazine and a fully automatic head magazine, with optional pallet changers, robotic tool magazines, and other automation modules, significantly reducing auxiliary machining time and improving overall equipment utilization efficiency.
The GMC2550wsμ is ideal for high-precision and high-efficiency machining of large structural parts and large molds.
The machine adopts a modular design with a moving table and moving beam configuration, providing excellent structural rigidity.
It is equipped with a self-developed, integrally cast, hardened rolling guideway system made of cast iron, whose high rigidity and low friction ensure superior linear and positioning accuracy.
A servo-driven constant-temperature control system guarantees long-term high-precision and stable operation.
The machine features a self-developed high-speed, high-torque mechanical spindle system and a wide variety of fully automatic attachment milling heads, with optional through-spindle coolant (TSC) capability to meet diverse application scenarios.
It is also equipped with a vertical-horizontal switching tool magazine and a fully automatic head magazine, with optional pallet changers, robotic tool magazines, and other automation modules, significantly reducing auxiliary machining time and improving overall equipment utilization efficiency.
The GMC2550wsμ is ideal for high-precision and high-efficiency machining of large structural parts and large molds.
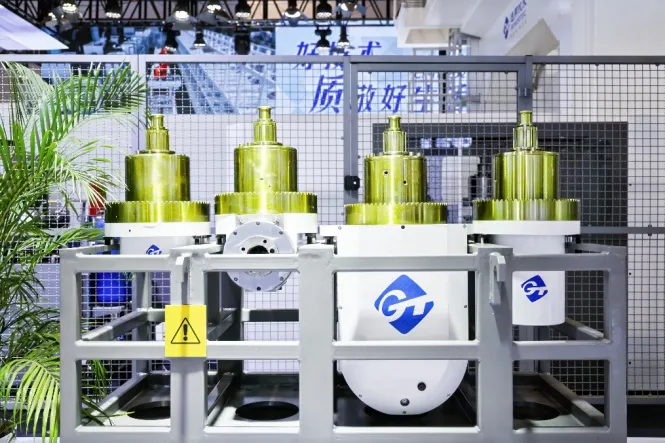
8.MGK7450×2H High-Precision Vertical Composite Grinding Machine
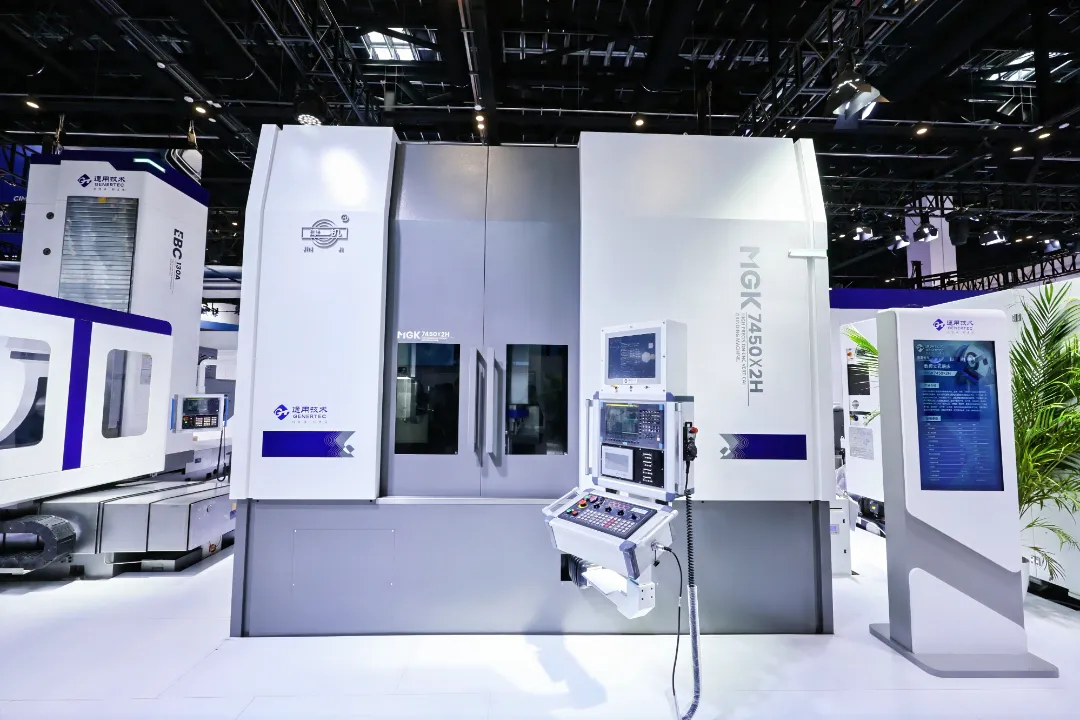
This machine features an integrated bed design, with a fixed structure for the bed, column, and crossbeam. Its well-balanced layout and high natural frequency ensure long-term stable operation of the machine.
The X-axis saddle and Z-axis slide are designed for minimal movement of components, providing superior control performance.
The worktable is driven by a self-developed hydrostatic structure torque motor, offering high precision and excellent rigidity, while effectively controlling manufacturing costs.
The machine is equipped with a tool magazine, online measurement, and grinding vibration detection functions, making it highly effective in complex machining scenarios.
The X-axis saddle and Z-axis slide are designed for minimal movement of components, providing superior control performance.
The worktable is driven by a self-developed hydrostatic structure torque motor, offering high precision and excellent rigidity, while effectively controlling manufacturing costs.
The machine is equipped with a tool magazine, online measurement, and grinding vibration detection functions, making it highly effective in complex machining scenarios.
9.M/1200V Vertical Coordinate Boring Machine
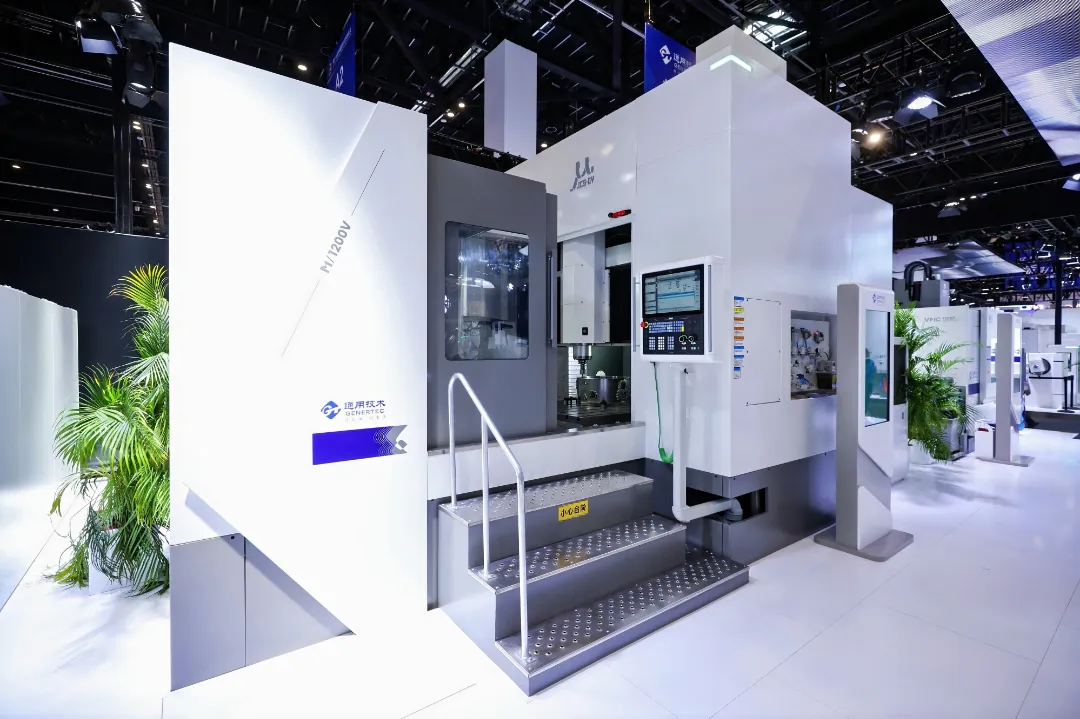
This product features a gantry-style moving beam structure with an integrated bed design. The entire machine is made from high-quality cast iron, optimized through finite element analysis to ensure high rigidity, stability, and excellent vibration resistance.
The linear axes are designed with high-precision rolling linear guides, and all mounting surfaces are hand-scraped to ensure exceptional accuracy of the machine.
The main heat sources, including the spindle, motor, and drive system, are equipped with a circulation cooling system, effectively ensuring the high-precision machining requirements of components.
The M/1200V is primarily used for precision finishing of parts such as precision boxes, plates, and multi-hole structural components.
The linear axes are designed with high-precision rolling linear guides, and all mounting surfaces are hand-scraped to ensure exceptional accuracy of the machine.
The main heat sources, including the spindle, motor, and drive system, are equipped with a circulation cooling system, effectively ensuring the high-precision machining requirements of components.
The M/1200V is primarily used for precision finishing of parts such as precision boxes, plates, and multi-hole structural components.
10.VDM866H Vertical Machining Center
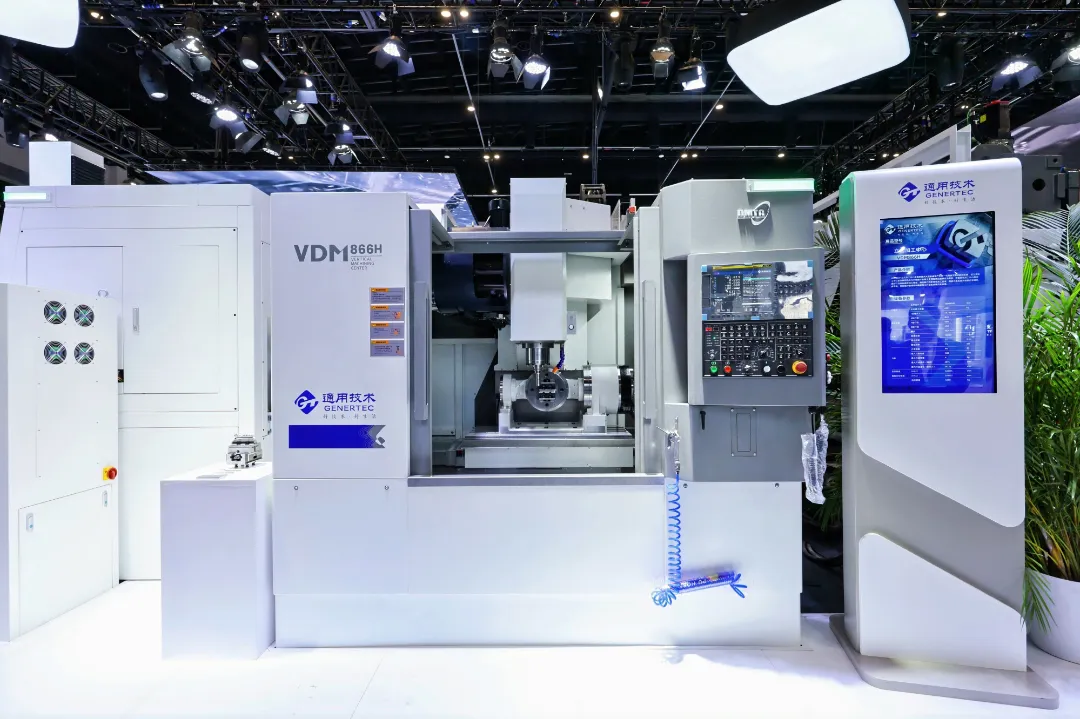
The VDM866H is designed for precision machining of difficult-to-cut materials such as titanium alloys. It features high precision, high rigidity, and high efficiency, making it suitable for multi-variety, small to medium batch, and high-precision machining scenarios.
The product adopts a modular design and is equipped with an 18,000 rpm central water-cooled spindle.
The linear axes are fitted with a full-process constant temperature cooling system, reducing ball screw thermal deformation.
It is equipped with a 40-tool shoulder-mounted chain-type tool magazine, ideal for multi-variety, small batch part machining.
The rotary axis uses a dual-torque motor rotary table with an absolute-type closed-loop system, providing high positioning accuracy and strong load capacity.
The product adopts a modular design and is equipped with an 18,000 rpm central water-cooled spindle.
The linear axes are fitted with a full-process constant temperature cooling system, reducing ball screw thermal deformation.
It is equipped with a 40-tool shoulder-mounted chain-type tool magazine, ideal for multi-variety, small batch part machining.
The rotary axis uses a dual-torque motor rotary table with an absolute-type closed-loop system, providing high positioning accuracy and strong load capacity.
11.Intelligent Flexible Machining Production Demonstration Line
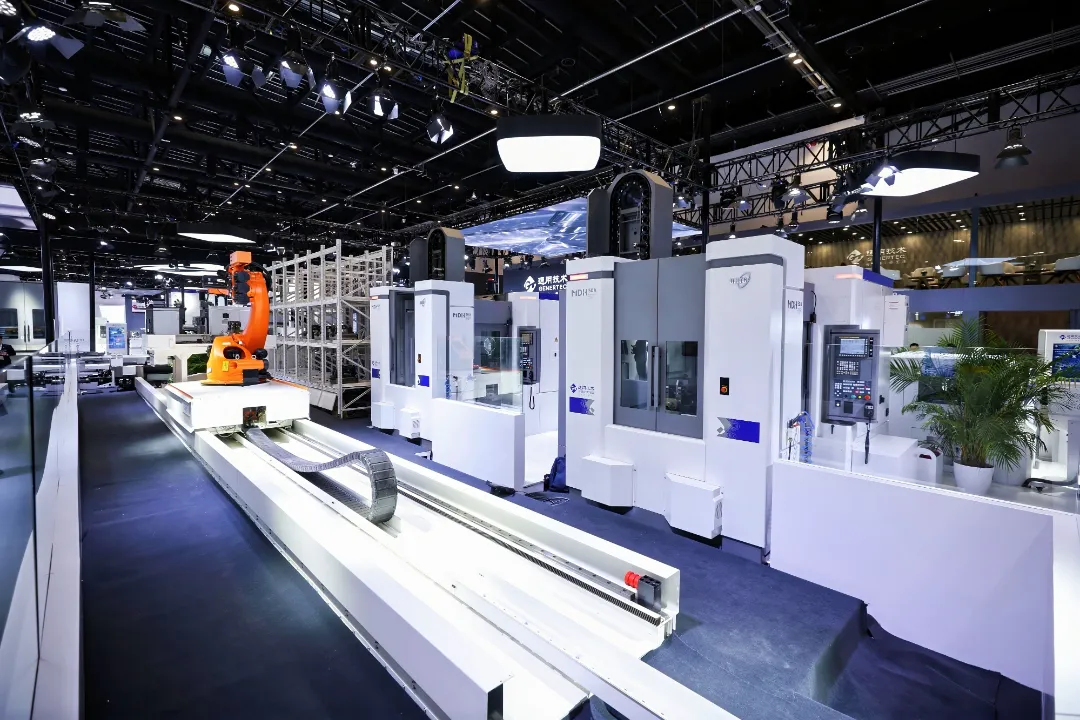
This production line adopts a modular design and provides a "one-stop" solution tailored to user needs. It is widely applicable to high-precision, high-efficiency machining of multi-variety parts in industries such as automotive, construction machinery, and industrial machine tools.
The entire line features self-developed horizontal machining centers and a custom-designed zero-point clamping system, supporting flexible and multi-model production on a single machine.
It utilizes modular agile logistics technology to meet the automation upgrade needs of users.
The system integrates an intelligent management and control platform, enabling smart, automated production across the entire line.
The entire line features self-developed horizontal machining centers and a custom-designed zero-point clamping system, supporting flexible and multi-model production on a single machine.
It utilizes modular agile logistics technology to meet the automation upgrade needs of users.
The system integrates an intelligent management and control platform, enabling smart, automated production across the entire line.
12.EBC130B CNC Plano Milling and Boring Machine
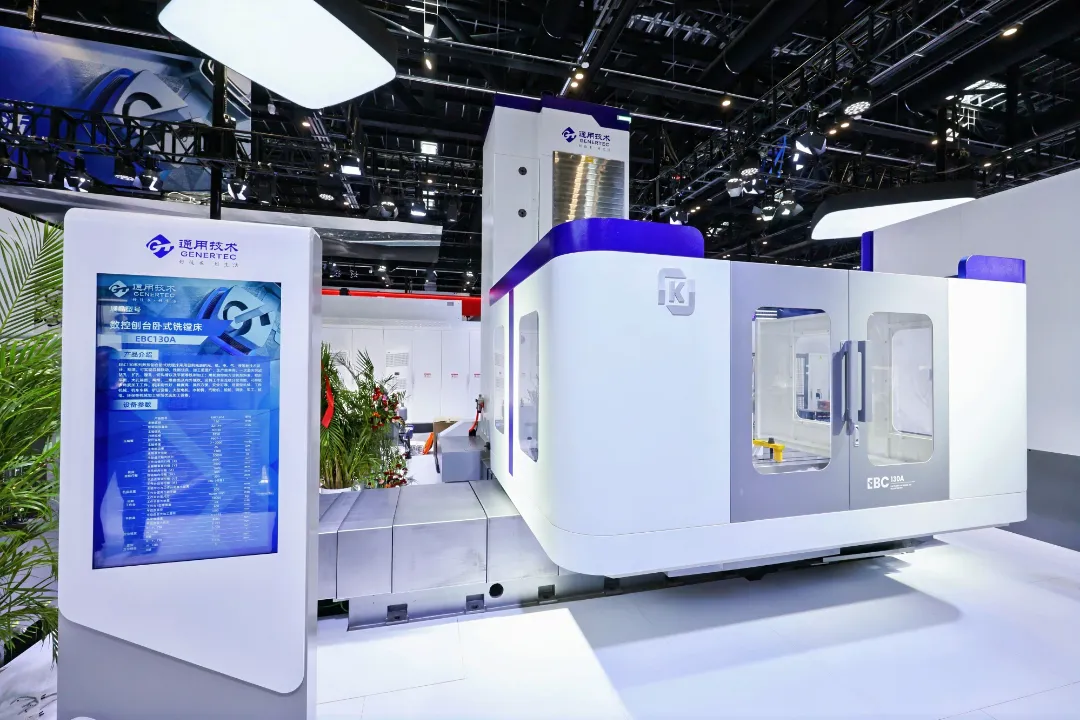
The EBC130B offers excellent performance, a wide machining range, and high production efficiency.
The machine's large components are made from high-quality cast iron, which undergoes secondary aging treatment to ensure superior rigidity.
The machine guideways feature a rolling-sliding composite structure, improving the contact rigidity of moving parts and providing excellent vibration damping with minimal high-frequency vibrations.
The surface hardness of the boring bar reaches HV900.
The machine's large components are made from high-quality cast iron, which undergoes secondary aging treatment to ensure superior rigidity.
The machine guideways feature a rolling-sliding composite structure, improving the contact rigidity of moving parts and providing excellent vibration damping with minimal high-frequency vibrations.
The surface hardness of the boring bar reaches HV900.
13.High-Precision 5-Axis CNC Spark Erosion Machine
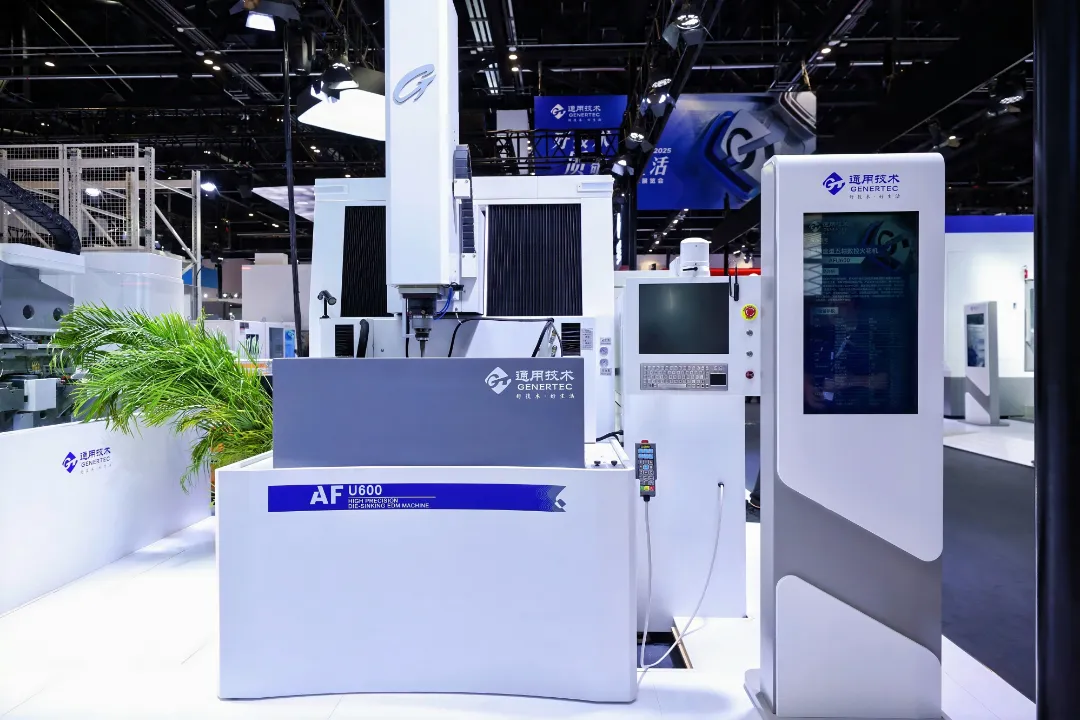
This product is a high-end machine developed for key industries, with independent intellectual property rights.
It features a bullhead-style structure and a closed-loop servo control system, enabling 5-axis simultaneous electrical discharge machining (EDM).
The newly developed low-loss, high-efficiency, high-power power supply excels in machining difficult materials such as titanium alloys and high-temperature alloys. It meets the machining requirements of parts such as discs and wheels that are otherwise inaccessible with conventional tools due to the overall flow channel's twisted geometry.
When machining mold steel, the surface roughness is Ra ≤ 0.08 μm, and when machining hard alloys, the surface roughness is Ra ≤ 0.15 μm.
It features a bullhead-style structure and a closed-loop servo control system, enabling 5-axis simultaneous electrical discharge machining (EDM).
The newly developed low-loss, high-efficiency, high-power power supply excels in machining difficult materials such as titanium alloys and high-temperature alloys. It meets the machining requirements of parts such as discs and wheels that are otherwise inaccessible with conventional tools due to the overall flow channel's twisted geometry.
When machining mold steel, the surface roughness is Ra ≤ 0.08 μm, and when machining hard alloys, the surface roughness is Ra ≤ 0.15 μm.
14.10,000 kN CNC Longitudinal Skin Stretching Machine (Model)
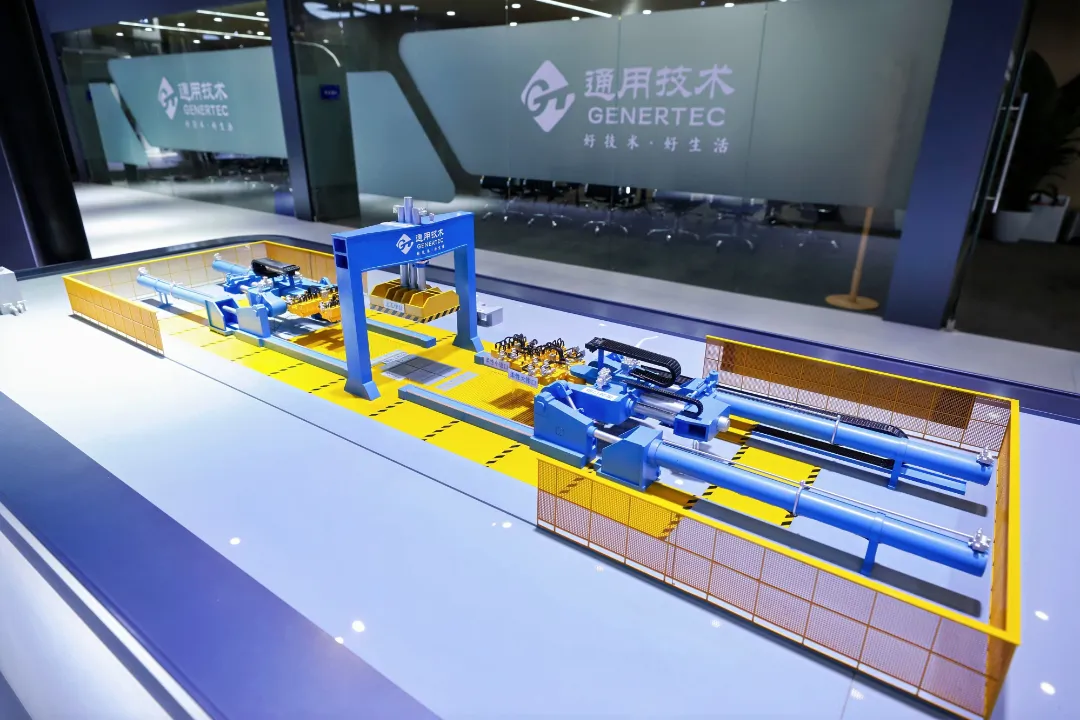
This product is widely used in the stretching and forming of sheet metal components in industries such as rail transit.
It features a fully closed-loop servo control system, leading the industry in position, pressure, and angle precision control. The position control accuracy is ±0.15 mm, speed control accuracy is ±0.1 mm/s, and multi-axis motion synchronization accuracy is ±0.15 mm/s.
The developed yield point detection and automatic tangent tracking functions have been granted national patents.
The custom CNC operating system allows real-time monitoring of the equipment’s operational status and includes multi-axis motion anti-collision safety protection.
The developed skin forming simulation system significantly enhances equipment efficiency and reduces product scrap rates.
It features a fully closed-loop servo control system, leading the industry in position, pressure, and angle precision control. The position control accuracy is ±0.15 mm, speed control accuracy is ±0.1 mm/s, and multi-axis motion synchronization accuracy is ±0.15 mm/s.
The developed yield point detection and automatic tangent tracking functions have been granted national patents.
The custom CNC operating system allows real-time monitoring of the equipment’s operational status and includes multi-axis motion anti-collision safety protection.
The developed skin forming simulation system significantly enhances equipment efficiency and reduces product scrap rates.
△ Grating Displacement Sensor
△ Independently Developed CNC System
△ Power Turret Automatic Tool Changing System / Tilting Rotary Table / Motorized Spindle
△ Ball Screws / Linear Guideways
△ Dual-Axis Tilting Milling Head / Single-Axis Tilting Milling Head
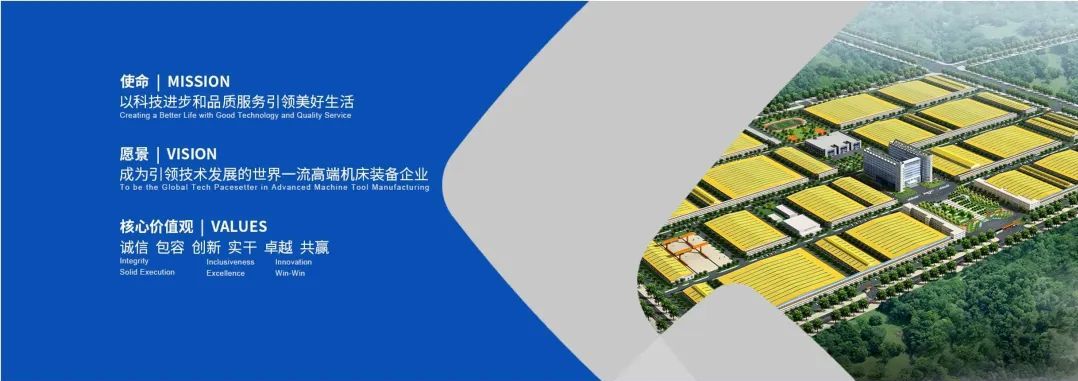
Need help finding a machine?
We will gladly assist you in making the right decision to achieve your business goals
Get a free Consultation